
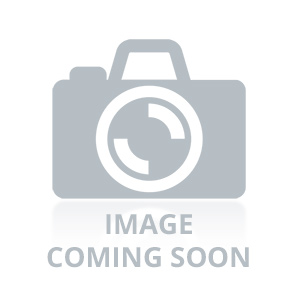
Using these simplified terms, viscosity may be defined mathematically by this formula: Its unit of measurement is dynes per square centimeter (dynes/cm2). It is referred to as shear stress and will be symbolized by F'. The term F/A indicates the force per unit arearequired to produce the shearing action. Its unit of measure is called the reciprocal second (sec-1). This will be symbolized as S in subsequent discussions. It describes the shearing the liquid experiences and is thus called shear rate. The velocity gradient, dv/dx, is a measure of the change in speed at which the intermediate layers move with respect to each other. Newton assumed that the force required to maintain this difference in speed was proportional to the difference in speed through the liquid, or the velocity gradient. Two parallel planes of fluid of equal area A are separated by a distance dx and are moving in the same direction at different velocities V1 and V2. Isaac Newton defined viscosity by considering the model represented in the figure above. Highly viscous fluids, therefore, require more force to move than less viscous materials. Shearing occurs whenever the fluid is physically moved or distributed, as in pouring, spreading, spraying, mixing, etc. The greater the friction, the greater the amount of force required to cause this movement, which is called shear. This friction becomes apparent when a layer of fluid is made to move in relation to another layer. Viscosity is the measure of the internal friction of a fluid. This places the instrument user in a position in which his own appreciation of the flow phenomena involved, coupled with the instrument manufacturer's "know how and experience", must be brought to bear.

Today's instruments vary from the simple to the complex: from counting the seconds for a liquid to drain off a stick to very sophisticated automatic recording and controlling equipment. The selection of the right viscometer from the scores of instruments available to meet the need of any application is a difficult proposition. There are many different techniques for measuring viscosity, each suitable to specific circumstances and materials. Rheological relationships help us to understand the fluids we are working with so that we can either know how they are behaving or force them to behave according to our needs. They know that viscosity measurements are often the quickest, most accurate and most reliable way to analyse some of the most important factors affecting product performance. Many manufacturers now regard viscometers as a crucial part of their research, development, and process control programs. Anyone involved with flow characterisation, in research or development, quality control or fluid transfer, at one time or another gets involved with some type of viscosity measurement. Viscosity measurements are made in conjunction with product quality and efficiency. Viscosity is a principal parameter when any flow measurements of fluids, such as liquids, semi-solids, gases and even solids are made.
